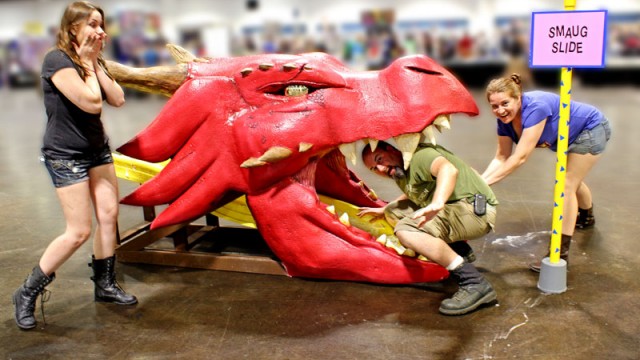
Roundtable Productions shares their process for several props created for a Live Action Show featured at Tampa Bay Comic Con 2014.
The Cake
Process:
Oversized cake wedges are cut from standard white styrofoam. The top and edges are coated with Free Form Habitat Epoxy Putty® to give the appearance of chocolate icing and create a durable shell. Then a basecoat of latex paint is applied, followed by a dark wash to give it a richer color.
The cherry is sculpted out of Free Form Air® to create a durable, yet lightweight prop that can be sanded to a smooth finish. It is primed and painted with a gloss finish.
The candle consists of a cardboard tube filled with Free Form Air® on each end to secure a steel wire that will be the wick. Free Form Air® is used for its strength and light weight. The drippings and flame are then sculpted with Free Form Sculpt®. The finished candle is primed and then painted.
The Foot
Process:
The foot is first carved out of standard white styrofoam. It is then coated in a shell of Styrocoat®. Any gaps are filled out with Free Form Air® and autobody filler. The details of the toenails and toes are sculpted in Free Form Habitat®. This allows for a more realistic texture to be sculpted, as well as adding strength and thickness to stand up to the abuse of the show. It is then primed with an epoxy primer and painted with latex paint to resemble the coloration of a large angry superhero.
A wall of faux bricks is fabricated out of vacuform panels and sculpted styrofoam to give the appearance of bursting out.
The Xenomorph Egg
Process:
The egg is carved out of standard white styrofoam and then coated in a scratch coat of Free Form Habitat®. This will allow us to build up the thickness and have better adhesion to the surface. The egg is then hollowed out and fitted with a bucket interior. To build up the thickness the outer surface is sculpted using Free Form Habitat® and any textures are stamped in during the curing period. Once cured, final details are added to the outside with more of the putty. A metal lathe is added to the top to create the “petals”. They are then coated completely in Free Form Habitat® and blended into the outside coat, as well as inside the bucket. A standard automotive primer is used, followed by latex paints.
The Xenomorph Egg is mounted on a base to give it a more impressive appearance. The inside of the bucket is thickly coated with Rebound 25® to create a fleshy, slimy interior. And the final gruesome touch is an icing of Dragon Skin® that creates the impression of mucus to make the whole thing glisten and look more alive. For the show, the egg is filled with water, slimy flora beads, water balloons, and a rubber spider. All of this makes finding the little orange flag a scary challenge.
The Dragon
Process:
The Dragon head is carved out of standard white styrofoam. The horns are shaped out of a metal lathe. The lathe is coated with Free Form Air® to provide a scratch coat that is strong and lightweight. The Free Form Air® scratch coat is covered entirely in Free Form Habitat® and a texture is stamped using rubber stamps made of Rebound 25®. Other horn details are also added by sculpting Free Form Habitat® directly over the styrofoam and textured stamped. The horns are masked off with tape and plastic to protect the detail. The head is then coated in a layer of Styrocoat®. Any gaps or lines are filled with Free Form Habitat and stamped with a texture stamp to match that of the Styrocoat®. This will be our skin texture. We also coated the teeth and parts of the jaw with Free Form Habitat® sculpted to the desired finish. More Free Form Habitat® is used to sculpt the detail around the eyes and add some selective scale details to the Dragon’s face. The entire head is primed and basecoats of latex paint are applied.
The basic details are then picked out in the desired colors. Shadows and highlights are airbrushed onto the skin. Added color washes, highlights, shading, and dry brushing are used to accentuate the details and make the sculpted textures stand out. On the day of the show, the head is fitted around a plastic slide that will be coated in shaving cream. The contestants will have to ride down the slide head first out of the Dragon’s mouth.
“Our team loved working on this project and it was great utilizing so many Smooth On products to achieve the end result.”
About Roundtable Productions:
Stefan Price is the owner of Roundtable Productions, LLC specializing in custom fabrication of props, sets, and effects for the entertainment industry. With nearly two decades of professional experience, ranging from Themed Attractions to Film and Television. He has earned two Bachelors degrees from the University of Central Florida in Mechanical Engineering and Theatre. His skills range from carpentry, sculpting, molding & casting, and metal fabrication to computer design and modeling, CNC operation, and 3D printing.
Roundtable Productions LLC
Providing Technical Entertainment Solutions
50 Brayton Rd., Winter Garden, FL 34787